Combinations of offices with laboratories, research and development spaces and/or manufacturing areas make life sciences facilities highly customizable. These multipurpose, technical spaces are in high demand from companies seeking first-class facilities for research-based advancements.
Low vacancies, high rents and the chance to convert unused office or retail spaces on a faster timeline have prompted some creative approaches to retrofit existing space to fulfill the needs of science and technology tenants. In other instances, facilities must be built from the ground up to conform to best practices.
But what factors matter most to the life sciences field? And how can developers increase their speed to market? Read on for tips and checklists for developers hoping to speed up the process of building or retrofitting these facilities.
Industry Drivers: Speed to Market and Flexibility
Office conversions into life sciences facilities offer a variety of options. Life sciences facilities often do not need to accommodate large trucks (eliminating circulation and loading dock concerns), they use office components and (most importantly) office conversions offer faster speed to market than other types of conversions.
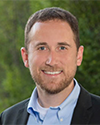
Charlie Yowell, Bohler
“Speed to market is most important for these developers/tenants. There is a shortage of space, so a well-designed, spec building will get snapped up quickly,” says Charlie Yowell, a Bohler principal in Raleigh, North Carolina.
Good manufacturing practices (GMPs) are the guidelines by which the U.S. Food and Drug Administration (FDA) ensures quality in the manufacture and distribution of pharmaceuticals, medical devices, food, cosmetics and more. Depending on the tenant, some life sciences facilities must be designed and constructed to meet these standards.
New construction can be better for facilities that require especially high clear heights or will have a high volume of trucks coming and going. However, some big box retail conversions may already offer high ceilings and loading docks, increasing speed to market.
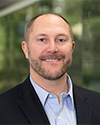
John Kucich, Bohler
Overall, offering flexibility is key for developers, explains John Kucich, PE, a Bohler principal in Southborough, Massachusetts. “Developers often begin construction on a project before tenants are locked in, so providing a facility that can be flexed into a variety of tenant operations is essential in an industry where customization of labs and office arrangement can greatly impact workflow.”
[box style=”4″]
4 Ways to Expedite Timeline and Get Marketable Facility On-Line Fast
- Perform thorough due diligence
- Garner Local economic development corporation (EDC) support
- Consider alternative permitting strategies
- Engage local design team including an architect and site civil engineer[/box]
Due Diligence Factors to Consider
Zoning
For conversions, Yowell advises avoiding zoning complications that might add unnecessarily to your timeline. “Assess zoning and establish a realistic entitlements timeline. If the use is allowed, entitlements and zoning will be faster than if the use is not allowed and a zoning change is required.”

Chris Dinoulis, Bohler
Understanding the surrounding zoning districts and existing uses creates opportunities, as well as an important responsibility for the developer, as Chris Dinoulis, an associate in Bohler’s Philadelphia office explains. “Being mindful of the project’s surroundings makes for a better ‘fit’. It’s important to take into account any potential requirements or concerns that may come from the adjacent community. Providing the flexibility for a site to incorporate measures to mitigate noise, improve visual impacts and promote safety can prevent a potential redesign and also go a long way in letting the surrounding community know you are looking to be a respectful neighbor.”
Utilities — Powering Research
“Connect with utility companies early on to understand their existing capacities and if any major upgrades are needed to their infrastructure. Find out if onsite water tanks or sewer pump stations are needed,” says Yowell. “This knowledge also helps to create realistic time and budget estimates,” as many facilities need high-capacity access to utilities and backups.
It is beneficial to engage a mechanical, electrical and plumbing (MEP) consultant early on, says Dinoulis. For example, at two recent, suburban Philadelphia life sciences conversion projects, Bohler worked closely with an MEP and the owner to identify utility demands needed for the project and upgrades to existing systems required for the tenant.
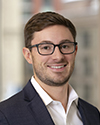
Zachary Richards, Bohler
Above all, says Zachary Richards, PE, a Bohler project manager in Boston, commit to understanding what tenants need. “Utility demand is very dependent on the tenant and type of operations. To create a flexible, marketable facility, engage an MEP or plumbing engineer to assess the existing systems and make recommendations that give developers a reasonable range of utility demands according to the tenant’s needs. These utilities can then be adapted to meet specific situations and recommend upgrades in the ‘Goldilocks’ zone: not too costly and yet sufficient for a wide range of tenant types.”
Conversions — Factors to Consider
Yowell explains that with conversions, architects can help assess the following important points:
- Clear heights — are they high enough for the potential tenants’ needs?
- Roof structure — can it support additional HVAC systems required for life sciences/lab/pharmaceutical use?
- Floor structure/depth of concrete — can it support the weight of equipment that will be utilized by potential tenants?
- Column spacing — is it wide enough for the potential tenants’ operations?
Richards elaborates on a common conversion layout, where advanced architectural planning saves on overall construction costs and results in a space well-suited for life sciences. “In the Boston area, we’ve seen office conversions that re-use the existing office space within a building and add an addition/expand the building into the often-underutilized parking lot area. In this new space, greater clear height can be provided, in addition to other tenant-specific design needs.
When working on a conversion, developers should assess other design factors like number of dock doors, height of loading docks, truck circulation, the condition of sidewalks and landscaping improvements. For example, with one suburban Philadelphia conversion project, Bohler helped the developer to understand the site layout and permitting impacts required to install a new loading dock that could accommodate an extremely large delivery truck. This loading dock was an unusual inclusion for life sciences buildings, but one needed for tenants with a substantial manufacturing component.
Richards also encourages developers to think through their tenant mix — how many different tenants could use the space and what will their operations be? If there’s an opportunity to have tenants share loading docks, this approach can also help to streamline conversions.
Ways to Expedite — Speeding Up the Timeline
Getting the right support is an essential part of planning well. Yowell advises developers to garner the approval of their local Economic Development Corporation (EDC). “Hold a preliminary meeting/discussion with the town and get the EDC or local civic groups on board with the project. These groups can help connect you to the right people, get meetings faster and expedite the overall process.”
In many locations, there’s not much resistance to life sciences projects, and municipalities often assist in expediting the process where feasible, explains Richards. “Tax revenue and economic growth are typically positives for the community. These facilities are usually developed on unused spaces that are either empty parking lots or vacant campuses that need revitalization anyway.”
And these spaces become even more attractive to tenants and the community when developers work with landscape architecture consultants to incorporate amenities and outdoor spaces to make facilities complement their surroundings.
Alternative permitting strategies can also help speed up a project’s timeline. Site civil consultants can expedite timelines by strategizing the entitlements process. “Some permits can be submitted before final design is set, and this can help to move the project along faster by allowing the contractor to get working in the field sooner,” explains Yowell.
This approach can assist with permits including mass grading, site clearing, early erosion and sediment control (E&S) permits, foundation permits and state sewage permits. For a ground-up pharmaceutical manufacturing facility in Durham, N.C., Bohler’s team obtained an early E&S permit, allowing the contractor to move forward while the final design and permits were completed.
“Success with these facilities depends on a proactive approach,” explains Yowell. “What does the potential tenant need, and how does that need translate into a plan of work that makes sense for the developer? We ask ourselves at each step how we can accomplish our goal to keep to a fast-moving timeline.” Just like with the life sciences facilities being built and converted — research and flexibility are key.
— By Sarah Daniels. Bohler is a content partner of REBusinessOnline. For more articles from and news about Bohler, click here.