The effects of sweeping macroeconomic forces in recent years are now manifesting themselves in industrial projects in Dallas-Fort Worth (DFW). And while the market still enjoys healthy fundamentals and tenant demand, the product being delivered now comes with a new look, functionality and set of requirements from end users.
To some degree, this paradigm shift in how industrial properties are conceived, designed and constructed stems from major economic factors and trends that are beyond the ability of architects, contractors and developers to control. To start with the obvious, interest rates are now five times what they were 18 months ago. When hikes of that magnitude are enacted so expeditiously, real estate professionals of all walks are impacted, even if it’s in an indirect manner.
“Demand for industrial space is there; if developers are building, the rents are probably there to cover those costs,” says Mike Williams, vice president of preconstruction at Dallas-based Talley Riggins Construction Group. “But for developers that are trying to form a team to get enough equity to get a loan — those deals aren’t working anymore with these rates. So paying extra close attention to who your clients are and their funding sources has been the biggest thing we’ve had to watch in terms of interest rates.”
Further, according to Dodge Construction Network, the volume of new construction on manufacturing projects increased by 285 percent from July to August as part of a 40 percent uptick in month-to-month nonresidential starts. That finding indicates a shift in the type of new product that is being demanded.
Lastly, for many users, the growth of automated technologies dictates the type of equipment and amount of labor needed within an industrial facility. Floor slabs, clear heights and parking allocations are among the design elements that are impacted by the extent and type of automation that an end user employs.
“Whether it’s for logistics, manufacturing or cold storage, every industrial project has four walls that are pretty similar — it’s the individual concerns and requirements of each end user that make them different,” says Patrick Holleran, senior principal at HDA Architects, a St. Louis-based design group that is active in Texas. “You have to be ready for automation in today’s world. Whether an industrial tenant currently has a lot of automation or not, it’s a topic that has to be broached. As the tenant’s needs may evolve, architects must design the facility in ways that can incorporate that automation should they need it in the future.”
The net result of these macro-level forces and happenings is a scenario in which users are needing less space. For industrial developers, which are typically paying more on their loan payments, insurance premiums and property taxes as part of the explosive growth of their asset class, that means less aggregate demand for space and therefore less overall revenue.
But there is also an element of self-inflicted activity within the new market dynamic. There is no faulting developers for developing, and hindsight is always 20/20. But the combination of several years of cheap capital and hyper-charged demand for industrial space undoubtedly contributed to oversupply of large-scale facilities in DFW.
“Today in DFW, there are about 15 industrial buildings of about 1 million square feet that are sitting vacant, and nobody in their right mind wants to add to that inventory,” says Bill Baumgardner, executive vice president of VanTrust Real Estate. “Even though tenant demand is still strong overall and there are some large requirements out there, speculative development is down about 60 percent year-over-year as of today. By the end of the year, it will be down 90 percent.”
The ebbs and flows of these trends may be standard over the long run, but these shifts can also create gaps, disruptions and market inefficiencies in the short run. But more to the point, what do these shifts in industrial design and development actually look like?
Scaling Down
For starters, newly delivered buildings tend to be smaller. Further, industrial architects and general contractors say that the development of huge speculative facilities that symbolized the meteoric rise of e-commerce and third-party logistics (3PL) is fading in the metroplex.
“Between 2018 and 2021, we did a lot of speculative industrial projects, but those have really dried up in favor of build-to-suits,” says Patrick Hazard, associate principal and team leader at Dallas-based Merriman Anderson Architects. “In addition, prior to COVID, the 500,000- to 1 million-square-foot cross-dock facilities were what users wanted. Now demand is shifting to smaller, more flexible rear-load product.”
“Larger buildings in excess of 500,000 square feet are few and far between unless it’s a build-to-suit, and that’s where a lot of the manufacturing growth is concentrated,” adds Williams of Talley Riggins. “But the shift from bigger to smaller projects isn’t just a function of higher interest rates, but also of supply and demand.”
To illustrate his point, Williams cites one of Talley Riggins’ 1 million-square-foot projects in DFW that he says was one of the only buildings of its size in the market when construction began. By the time the job was wrapping up, he says a dozen other buildings of similar size were under construction. None had leases in place.
Lenders, which not so long ago battled among themselves to finance these 500,000- to 1 million-square-foot facilities, have begun to shy away from large-scale spec deals. That isn’t shocking given that loan origination volumes are down drastically across the board. But sources say that there’s still appetite for industrial allocations — just for a different product type.
“There’s more interest in shallow-bay, flex product — anything under 250,000 square feet — as large-scale spec developments slow to a trickle,” says Trevor Heaney, principal at Dallas-based ARCO/Murray Design Build. “There’s no more free money out there, and as a result, developers are now much more cognizant of their carry costs. Plus we’re in an environment of expanding cap rates. All of these factors have to be taken into consideration early in the project life cycle.”
“Banks don’t want to lend on larger buildings, and institutional buyers don’t want to buy larger buildings right now,” concurs Baumgardner. “They’re focused on smaller assets, and with the spec spigot mostly turned off, capital is flowing to build-to-suits.”
As an anecdotal sign of the times, Baumgardner says that VanTrust has a site in Terrell, an eastern suburb of Dallas, that is fully approved for up to 1.2 million square feet of industrial development. But the company is sitting on the dirt for the time being due to both high rates on construction loans and limited demand for facilities of that size.
“We’d love to be able to do all 200,000- to 250,000-square-foot buildings or 500,000- to 600,0000-square-foot buildings because we still see demand at those levels, but we have to watch the market,” he says. “We’re not shying away from getting land inventoried to do the larger buildings, but we’re having success with putting buildings of different sizes out there and just playing to the strengths of the site and the submarket.”
Some recently announced projects in the metroplex speak to this trend. For example, Fort Worth-based Street Realty just announced the development of West Loop Business Park, which will consist of 14 shallow-bay buildings that will all span 9,900 square feet. At 140,000 square feet, the total footprint lies in the wheelhouse of what today’s users want. In addition, the sub-divisibility of the buildings to suites as small as 975 square feet speaks to tenants’ penchant for flexibility.
The Power of Power
Access to a critical capacity of electricity at an objectively affordable rate is a major consideration in most industrial deals, and Texas has always counted that feature among its draws for industrial users.
The winter freeze of 2021 exposed some of the problems of relying on a deregulated grid, but sources say that in the context of industrial leasing, it can be both helpful and detrimental. Essentially, a local provider’s ability to deliver the capacity of power that a user needs can make or break a deal, and architects and contractors must factor this requirement into a variety of the design and build plans.
For example, to re-invoke the concept of automation, many e-commerce facilities use robots to sort and pick various items. Hazard of Merriman Anderson explains how that particular feature impacts specific design and construction elements in terms of both physical space and electrical infrastructure.
“Column spacing is impacted by robots in certain facilities that have ‘smart floors’ that are GPS-ed,” he says. “These floors have linework that robots follow to get to whatever bin, shelf or rack they pull product from and take it to the handling area to be packaged and sent out. You want to make the space more open so robots don’t have to work around columns. But robots also need to be charged, so we have to make sure that in terms of the base of the building design, we are providing for charging stations and amperage that’s needed for that.”
The profiles of the trucks and vans that distribute product also have implications for industrial design. Whereas a few years ago during the e-commerce explosion, all the noise was about self-driving cars and whether truck court depths could be shrunk to take advantage of automated maneuvering, developers today are looking at electric vehicles (EVs) and their needs as a potential game-changer.
Baumgardner of VanTrust points to an Amazon project in El Paso that fell through due to insufficient power supply for distribution vehicles. The central issue involved the desire of the e-commerce giant, which has pledged to reach net-zero carbon emissions by 2040, to utilize an entirely electric fleet of delivery vehicles.
As the developer, VanTrust accommodated the client’s request and wired all the parking lots with the necessary infrastructure to keep the fleet charged and ready to roll. But the local power company simply didn’t have the capacity to supply the amount of juice Amazon required. The deal effectively died there, Baumgardner says.
“Some of these users like FedEx and UPS that are moving toward EVs — some sites may not be able to support their power needs, so that’s a big design element that everybody’s looking at right now,” Baumgardner says. “Developers need to do upfront research on whatever provider covers the area and make sure they have the capacity to deliver the amperage they need and understand how long it will take to deliver it.”
“If our clients aren’t installing electric vehicle chargers for cars and trucks from the outset, then they’re getting the conduit in place so that it’s ready and available as soon as the requirement is there,” adds Heaney of ARCO/Murray. “It’s all about understanding our client’s businesses, identifying today’s requirements and designing projects that are cost-effective today and ready to receive the widest range of tenants in the future.”
As a final note on design implications of vehicles and the spaces that house them, space for trailer storage is still very much in high demand, according to Williams.
“Buildings under 200,000 square feet tend to have built-in trailer storage with the ability to expand by an extra 100 or so stalls,” he says. “That may seem like an excessive amount of trailer positions for a building of that size, but from a development standpoint, it can become a secondary stream of income to rent those spaces out or appeal to a larger pool of tenants that may have that need.”
Sources interviewed for this story generally concurred that among products still hit by supply chain disruption, electrical gear like transformers and switchboxes are the current poster child. A number of sources also said that industrial development sites that can comfortably deliver large amounts of power are highly coveted by data center companies that have even larger energy footprints than traditional industrial users. And if the price is right, sometimes that’s what those sites end up housing.
Aesthetic Importance
With the growth of industrial real estate has come a concentrated push into more urban settings. E-commerce and third-party logistics users, in particular, place a premium on proximity to customers, as transportation comprises a significantly larger portion of their operating costs than do real estate expenses.
To that end, municipal leaders and local residents have begun to demand and expect a certain level of aesthetic with these projects. Simply put, if industrial projects in urban and residential areas tend to be eyesores that locals dislike, they’re much less likely to get the bureaucratic support they need to be built.
In addition, beautifying these buildings on the outside and equipping them with more inviting features on the inside tends to be beneficial from the standpoint of employee recruitment and retention.
“The construction boom in Texas has pushed more neighborhoods closer to these industrial facilities, and nobody wants to look out their window and see a cold gray box,” says Heaney. “So you’re seeing a significant increase in design requirements that is being manifested on the façade through reveals, offsets, height variances and coping, along with more glazing on the front and façade of these buildings. You’re also seeing very highly designed and aesthetic awnings placed across the fronts of these buildings.”
“We’ve got a lot of tools and tricks we can utilize to achieve the high aesthetics on these facilities,” he continues. “Externally, another requirement we’ve seen increase in importance, both from municipalities and users, are landscape requirements. We’re designing these properties to ensure that projects fit into neighborhoods and aren’t just the infill industrial facilities of old.”
Much like traditional elements such as column spacing, clear heights, floor slabs and electrical infrastructure, successfully designing for aesthetic appeal comes down to understanding all the nuances of a client’s operation and goals.
“It’s critical to understand the client’s business and history, along with where they’re at now, where they want to go and how they want to incorporate those elements into their new facility,” says Holleran. “You can customize the interior and exterior design and flow of the warehouse based on that. It just takes time to get to know their needs.”
HDA Architects recently completed a 28,000-square-foot, build-to-suit expansion and renovation in Brenham, about 75 miles northwest of Houston, for Mike Hopkins Distributing. As part of the project, the company commissioned a custom-painted wall mural of the alcoholic beverage distributor’s logo on the building’s exterior.
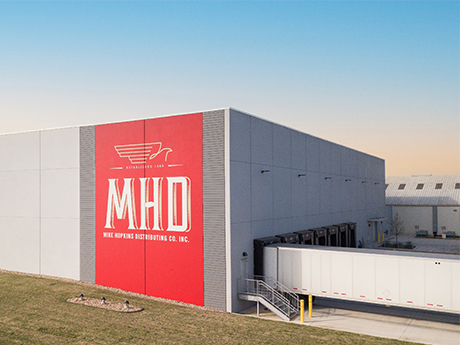
As part of the expansion and renovation of Mike Hopkins Distributing’s industrial facility in Brenham, HDA Architects commissioned a mural of the company logo on the side of the building. In addition to furthering existing marketing and visibility initiatives, the mural enhances the project’s aesthetic appeal, a growing prerogative within industrial design.
“There are cool things you can do that don’t cost a ton of money like painting a mural on the warehouse — it’s visible from the highway and is great branding for the company that stands out as a design element,” notes Holleran. “Some clients don’t care about that, but aesthetics do tend to be important to municipalities. Again, it starts with conversation and getting to know their needs and requirements. You want to represent your client’s goals but also design a building that the city will be proud of as well.”
Hazard says that the emphasis on high aesthetic quality is not limited to major urban districts.
“Even with sites that are on the outskirts of town, those cities are becoming more sophisticated and developed and want elegant design,” he says. “Industrial buildings are no longer just four concrete walls and a roof. Now these projects involve making sure we’re hitting vertical and horizontal articulation to create visual interest so it’s not just big slabs and walls. Cities can also enforce mandates on certain types of materials that enhance visual appeal.”
Closing Thoughts
Despite the various shifts that are forcing developers and users to adjust their approaches to new projects, the business of designing, constructing and operating industrial facilities in DFW remains very attractive due to the metroplex’s exceptional record of job and population growth.
“The biggest advantage in industrial design right now is that everyone is moving to Texas,” says Hazard. “There’s real demand for industrial product, and we have the ability to accommodate it, whether that’s by expanding footprints within the metroplex or finding hidden spots that are near urban cores but might be more difficult sites to
develop.”
Seasoned real estate veterans also note — not incorrectly — that the consumer preferences that drove these changes in industrial design and functionality are always shifting unpredictably. Change is always a constant. At present, that change is taking the form of smaller footprints, but that doesn’t mean that the ability to plan for future expansion isn’t still critically important.
With developers now delivering and tenants now demanding smaller buildings, it should be easy in theory for users to downsize their operations and find smaller spaces at semi-affordable rents. But once those facilities are absorbed, and once industrial operators have better grasps on their automation needs, the pendulum may begin to swing in the other direction.
In that sense, and given the metroplex’s track record for robust growth, it’s critical to bake contingencies for expansion into design and development plans.
“Every project has to be designed for future use, meaning it’s designed in a way that the asset remains valuable even after its current use,” says Holleran. “Automated storage and retrieval systems that eliminate labor and other features like that dictate some of the design. So you design from the inside out while always looking at column spacing and clear heights and materials with an eye for future expansion.”